Building supplies shortages: 'I can't see it getting better any time soon'
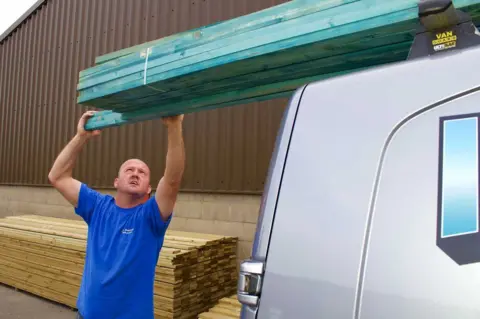
The House Builders Association says the construction industry currently faces huge shortages of materials, massive delays and significant price rises. How are those involved in the industry coping and can they see any light on the horizon?

'People don't want to be waiting without a roof on'

Craig Barnett, a builder based in Dereham, Norfolk, says the current situation with obtaining materials is "probably the worst it's been" in his career.
"Getting hold of the building materials is the main thing," he says. "With bricks, we are on a 26-week lead time."
He says he is having to include projected price increases in any quotes he gives.
"They [prices] are moving up. Hopefully they will come down - but the prices on quotes are higher than normal now."
A home extension that might normally cost £20,000, he says, currently costs about £26,000.
"We are having to do a lot more organising with builders' merchants and trying to work with them to get the stuff," he says.
"If you don't do that, it will put you behind and people don't want to be waiting without a roof on or windows in."
Bricks and blocks are the hardest items to get hold of, he says, followed by roofing tiles, which currently have a 16-week lead time.

'I can't see it getting better any time soon'
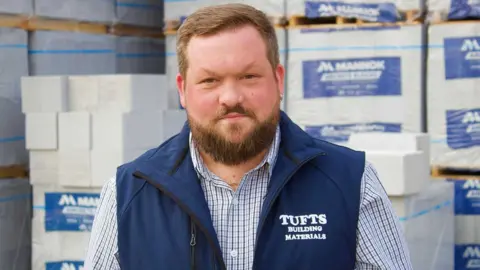
Mr Barnett's difficulties are understood all too well by Liam Brydon, general manager at George Tufts and Son, a builders' merchant at Bradenham, Norfolk.
"It is bad," says Mr Brydon. "It is a real challenge to get the materials in and to make sure we've got enough to keep everybody going and to keep their projects on the move.
"We are having to tell people there is a lead time on some products and that not everything is readily available like it used to be.
"Sometimes people are having to factor that in when they are doing their projects."
"The biggest issues we having are with bricks, blocks, timber and roof tiles. They are the four biggest problems at the moment which we are trying to manage."
He says he has ordered one batch of bricks that is not expected to be delivered until the middle of 2022.
"We are trying to stay really close to our customers so we know what projects they have coming up and we know what materials they are going to be using," he says. "We are trying to stay ahead with what they need.
"There are a lot of things that are now not going to come until next year so I can't see it getting better any time soon."

Analysis: Andrew Sinclair, BBC Look East Political Correspondent
MPs are returning to Parliament knowing that the issues of shortages will be one of the big talking points this term.
Whether it's building, haulage, hospitality, the NHS or the supermarkets, I'm told constituents are complaining in large numbers that they just can't get the staff or the goods they need.
Brexit is an issue - it is much harder to employ EU workers nowadays - but Conservative MPs are quick to point out that there are a lot of other issues at play. Covid forced many EU nationals to return home and they haven't come back. It's also responsible for delays in training new drivers and staff.
And when it comes to haulage, this is an industry that has always struggled to attract and retain staff: before the pandemic there was already a shortage of 60,000 drivers.
The government has allowed HGV drivers to work longer hours and agreed to fund more training but it won't grant temporary work visas to drivers from the EU.
No-one is expecting this problem to end soon; indeed, the Confederation of British Industry (CBI) has warned that shortages could be with us for the next two years.

'We've got really no idea when they are going to be able to supply it'
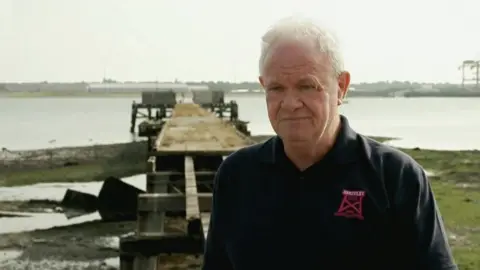
Supply shortages are not just affecting house builders.
About 60 miles (96km) south of Bradenham, in the Suffolk village of Shotley, supply issues are also hampering efforts to restore a pier that sits at the meeting point of the Orwell and Stour estuaries.
The community enterprise behind the restoration project has been hit by a triple whammy of issues. First, Covid 19 saw construction work on the project stopped. Now, supply issues are holding back the works. The third issue has been the rapidly rising cost of timber.
John Davitt, chairman of the Shotley Heritage Charitable Community Benefit Society, says the aim had been to get Shotley Pier finished and reopened for the start of summer.
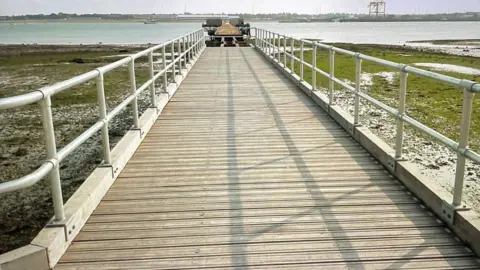
As autumn knocks on the door, the pier remains unfinished.
"What's delaying us now is the final touch.... the mesh at the bottom of the railings which is a requirement both of health and safety and our insurers," Mr Davitt says.
"That has been delayed by three weeks. We've got really no idea when they are going to be able to supply it."

'It is terrible'
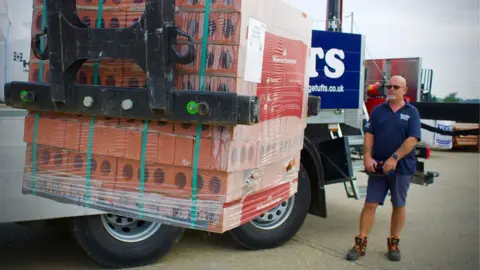
"It is really tough out there," says Rico Wojtulewicz, head of housing and planning policy at the House Builders Association.
"It is terrible. We are seeing such huge shortages of all sorts of materials, massive delays, a lack of any ability for builders' merchants to replenish their stock, prices are going up, projects are being delayed, contracts are not being met.
"This year we've seen a 20% inflationary rise on the cost of materials and the difficulty is there are so many people competing for these materials."
A key part of the problem, he says, is a peculiar split between the demand and supply of building materials.
On the one hand, he says, the number of building projects actually increased during the Covid pandemic, creating a surge in demand.
On the other, the pandemic reduced the ability of materials firms to produce their products.
There is now a gap between those needing building materials and the ability to create them.
"It should improve next year because a lot of material producers are starting to get back to full capacity," he says,
"It has become really difficult to ensure you have enough materials for an entire industry."

Find BBC News: East of England on Facebook, Instagram and Twitter. If you have a story suggestion email [email protected]