Building projects hit by lack of supplies and price rises
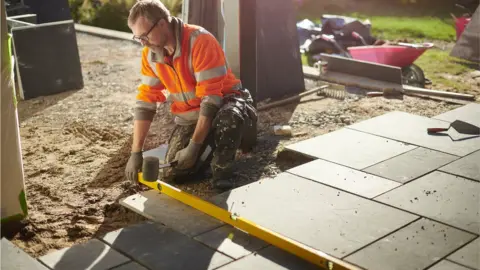
Building materials are running short in the UK, leaving DIY projects in doubt and building companies under pressure.
The Construction Leadership Council has warned that cement, some electrical components, timber, steel and paints are all in short supply.
It blamed "unprecedented levels of demand" that are set to continue.
The Federation of Master Builders said that some building firms may have to delay projects and others could be forced to close as a result.
"Small, local builders are being hit hardest by material shortages and price rises," said chief executive Brian Berry.
"We can't build our way to recovery from the pandemic if we don't have the materials."
Roland Glancy, managing director of design service Peek Home, advised people to delay home improvement projects until autumn.
"The last thing you want is to knock through a wall and then struggle to get hold of a bag of plaster to complete your vision leaving you living in a building site, just when we should be enjoying our new freedoms," he said.
Prices rising
The supply problems stem from a number of factors. Construction industry projects have surged since lockdown began easing which has led to skyrocketing demand for already scarce materials.
There are also issues hitting specific products, such as the warmer winter affecting timber production in Scandinavia while the cold winter weather in Texas affected the production of chemicals, plastics and polymer.
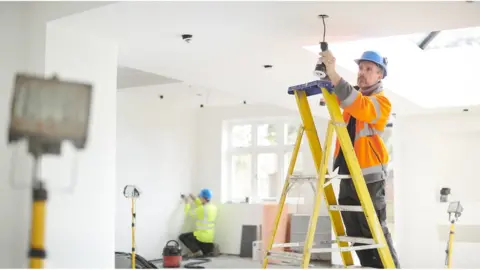
There has also been a sharp rise in shipping costs, said Noble Francis, economics director of the Construction Products Association.
"Shipping costs have risen sharply due a shortage of empty containers from Covid-19-related issues and the sharp recovery in global demand," he told the BBC.
For instance the cost of shipping a 40ft container from Asia to Northern Europe soared from $1,500 (£1,061) in summer 2020 to more than $8,300 (£5,873) by May 2021, he said.
With demand globally increasing and the UK importing many of its raw materials, lead times for orders are lengthening while prices are shooting up.

'I'm being quoted £10,000 for a £5,000 bathroom job'
Mohsen Kashan of Milton Keynes has been waiting nine months to have his bathroom renovated after a leak.
But with problems getting parts and tradespeople he told the BBC he now simply can't afford the rising costs he is being quoted.
"It's a simple job for a small bathroom just 2 metres by 2.5 meters. But we have been quoted £10,000 for what used to be less than £5,000.
"To expect to pay between £8,000 and £10,000 for a small bathroom seems too much," Mohsen said.
He's been struggling since September to get the repairs done.
"We've tried B&Q, a couple of other stores, as well as installers and half a dozen fitters.
"Either the cost of the materials has been too high, the cost of labour too high or materials are simply unavailable."

The Office for National Statistics has projected a rise of 7-8% in material prices, with increases for certain materials, such as timber, expected to more than double during the course of the year.
"My members are experiencing price rises of 10-15% across the board, rising to 50% on timber and 30% on cement," said Mr Berry.
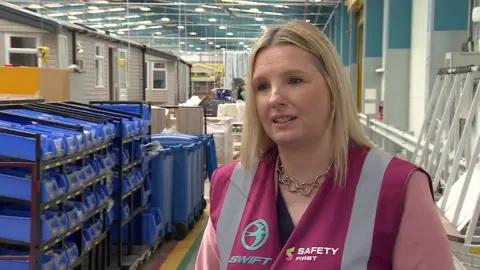
'Unprecedented demand'
"It is really challenging in terms of supplies. It's nothing that we've ever experienced before," said Amy Archer, deputy managing director of the Swift Group, based in Cottingham near Hull, which makes caravans, motorhomes and holiday homes.
She said there are two issues: "The first is a shortage of materials in the first place and the delays that we've seen through the ports because of shipping container shortages."
The second is rising prices: "Commodity prices are going up because there's such a huge demand for products."
Booming activity domestically hasn't helped too, she said. "Lots of people are doing home improvements such as new kitchens and that's all draining the materials that are available."
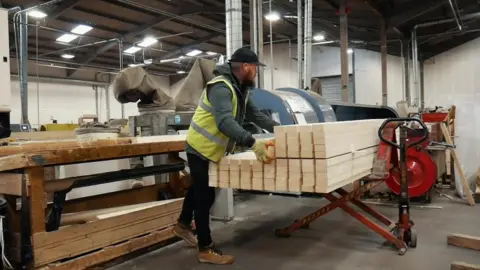
"This really is unprecedented," said Chris Husband, commercial director at wood supplier Bayram Timber. "The sheer volume of timber that's being demanded at the moment, they are struggling to keep pace with it in Scandinavia, where we source most of our raw material."
His company, based in North Ferriby near Hull. competes against others across the globe for the timber and is "having to wait in line", he said. "It's having a huge inflationary effect on the raw material price and obviously the lead times as well."
Is the current situation here to stay? "We're pretty much certain that this is with us for the rest of this year," he said.
Brexit effect
Brexit has also affected the UK's timber supply as 80% of softwood comes from Europe, said Thomas Goodman, construction expert, from MyJobQuote.
Steel is also in short supply, as global demand exceeds supply. "Many steel manufacturers have stopped taking orders, as they are worried that panic buying will result in extremely low stock," he said.
The shipping costs issue is likely to subside in the next three to six months but global demand is likely to remain high for the next six to nine months, predicted Mr Francis.
Mr Berry pointed out that small builders can't stockpile or plan jobs far in advance, unlike larger firms, so they need to be assured that the materials will be at the merchants when they need them.
"Consumers must be aware that shortages are causing delays to projects, and that costs may change in the months ahead because of this pressure," he said.
Building materials supplier Travis Perkins said: "In instances where we have seen some challenges posed by global demand for raw materials or inflationary pressures, we continue to work closely with our suppliers and partners to ensure healthy stock availability for our customers."
But with higher material prices for the moment, many homeowners and builders are choosing to delay work until the necessary resources become more affordable.