The T-shirt chewing enzyme ready to tackle plastic waste
In 2010, researcher Sintawee Sulaiman had just started her first lab job, at the University of Osaka in Japan.
She was tasked with modifying and experimenting with an enzyme that her colleagues had discovered in a pile of rotting leaves in the park next to the university, called LCC - leaf-branch compost cutinase.
LCC helps microbes break down the waxy coating of leaves, and Ms Sulaiman hoped it might also help degrade plastic.
One afternoon, she cut up some plastic packaging from a pair of headphones and left the shards in water overnight with some samples of LCC. By the morning, it looked different.
"The piece of plastic had some holes, or some breakdown," she recalls. "That made me feel so surprised."
The plastic was PET, which is a polymer - a long molecule in which smaller chemical units called monomers are joined tightly together.
Polymers are found everywhere in nature - cellulose, a structural component of trees and other plants, is the most common example.
Enzymes have evolved alongside them to break down their chemical bonds, allowing microbes to biodegrade organic material.
But enzymes have only been exposed to plastics for a few decades, which is why the materials don't degrade. However, over the past two decades scientists have found a way to give evolution a helping hand.
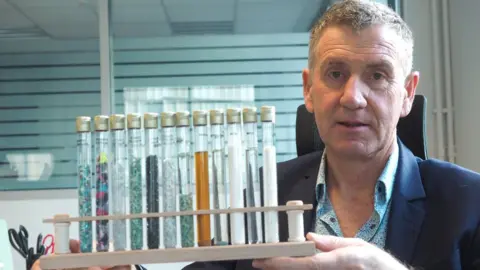
That's what Prof Alain Marty and his colleagues at the University of Toulouse in France have been doing.
Over eight years they re-engineered LCC - now LCCICCG - to become a trained PET specialist.
The enzyme is now so efficient that it can completely break the PET polymer down to its constituent monomers - the chemicals producers need to make new plastic. Prof Marty likens it to breaking apart a pearl necklace.
"We are using an enzyme that you can consider a molecular scissors," he says. "We break down the link between the pearls, liberate the pearls and in this way, after purification, we can sell these pearls again."
He is now the chief scientific officer at Carbios, which has a demonstration plant in Clermont-Ferrand, in central France.
It looks a bit like a microbrewery, with a large cylindrical reactor surrounded by other equipment for processing PET plastic.
The biggest machine of all processes polyester-rich clothes. Polyester, a form of PET plastic, accounts for about half of the clothing fibre the world produces.
Eventually, most of these clothes end up being incinerated or sent to landfill, often in the developing world.
But the big machine in Clermont-Ferrand offers them an afterlife, shredding them and then meticulously removing buttons and sequins.
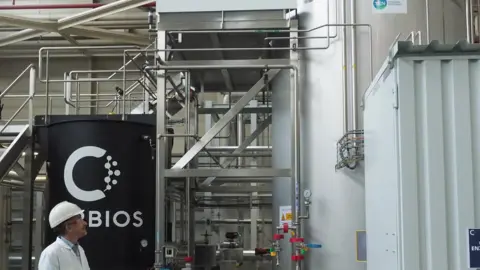
The scraps of fabric that make it through this process are then fed into another machine where they are turned into soft pellets. Mountains of jewel-like shards from plastic bottles go through the same machine, also to be turned into pellets. This step increases the surface area of the material and weakens the molecular bonds of the plastic.
Importantly, the pellets do not need to be 100% PET. The pellets from textiles contain other fabrics like cotton and the bottles contain green dyes. Mixed plastics, such as food trays, can also be dealt with.
The company is now about to radically scale up operations. By 2025 the plan is to open a factory in northeast France that will be able to recycle 50,000 tonnes of PET waste a year - that's 300 million T-shirts, or two billion bottles.
Carbios does not aim to become a recycler, but will license its process out to other companies, which means it has the potential to spread quickly. They have formed a consortium with big brands including Nestle, L'Oréal and PepsiCo.
Since it produces the same chemical monomers that plastic producers are already using, minimal change is needed.
But the familiarity of its product is also a challenge - since these indistinguishable chemicals will cost about 60% more than those derived from petrochemicals.
"With time Carbios will get access to more and more feedstock," says Emmanuel Ladent, Carbios chief executive.
"So the cost of raw materials will go down, because we have access to feedstocks which today are incinerated or go to landfill."
He adds that any future carbon tax will also benefit them.
Carbios are not alone in this sector - other research teams are working on PET recycling with a variety of enzymes.
But none of these teams are at the point of scaling their process up.
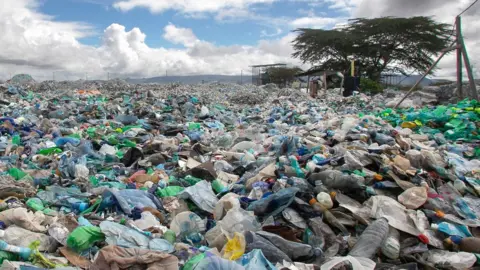
"I'm really enthusiastic about the work that Carbios is doing, because they are kind of blazing the trail if you like," says Prof Andy Pickford, from the Centre for Enzyme Innovation at the University of Portsmouth. "If people can see this works, then hopefully more people will buy into it."
But he adds that he is less optimistic for recycling other plastic types. Some may never be able to be recycled, and we may do well to move away from using these plastics.
Any progress would be welcome - according to the OECD, less than 10% of plastic worldwide is recycled. Every year, around half of the world's 400 million tonnes of plastic waste goes to landfill.


Carbios is already turning its attention to plastics with more complex chemical structures. Nylon is top of the list, but Prof Marty tells me this will need a completely different enzyme to unlock it.
Meanwhile, Sintawee Sulaiman, who first witnessed LCC degrade plastic in 2010, is pleased with the progress her enzyme has made since she gave it its first meal of headphone packaging.
"I feel very lucky to have met LCC," she says. "And I really hope that it can help the world - to change the world into a better place."