Where EV batteries go to die – and be reborn
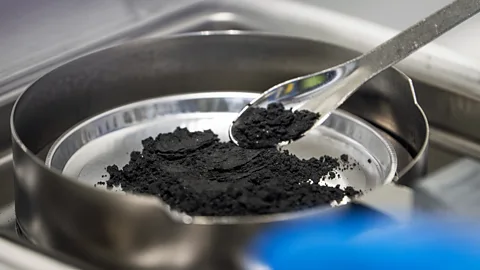
Batteries for electric vehicles are notoriously difficult to recycle, but growing demand for the rare metals they contain is leading to innovative new ways of retrieving them from used power cells.
I am standing in a lab where batteries go to be reborn. But first, they must be shredded.
What arrives here is a dark powder called "black mass" – a substance derived from pulverising batteries almost to oblivion. Each particle is less than a millimetre across. Staff working for Altilium, a recycling firm in the south-west of England, are now tasked with extracting crucial materials from this pitch black disorder.
The powder contains some plastic and steel from the battery which must be separated out, but there are also sought-after materials such as lithium, nickel, cobalt and graphite. These are the prized ingredients with which the lab workers here can make a new battery.
As the climate crisis intensifies, the world is electrifying. Countries are increasingly shifting away from fossil fuels towards renewable sources of energy including solar panels and wind turbines. Homeowners are installing heat pumps in the place of old gas or oil boilers. And drivers are increasingly buying electric vehicles (EVs) powered by batteries.
According to the International Energy Agency (IEA), nearly one in five cars sold in 2023 was electric. This was a 35% year-on-year increase compared to 2022 and brought the number of EVs on the world's roads to 40 million. The problem with this is that demand for batteries, and the materials required to make them, is soaring.
"One of the big challenges is that the minerals are kind of concentrated in certain places," says Christian Marston, president and chief operating officer of Altilium. Over half of the world's nickel comes from Indonesia, while two-thirds of all cobalt comes from the Democratic Republic of Congo – both of which have ongoing human rights issues associated with mining operations.
That's why there's now a race to find other ways of sourcing those key minerals. Recycling batteries is one option, but is also notoriously difficult. Staff at Altilium, however, say they've cracked it.
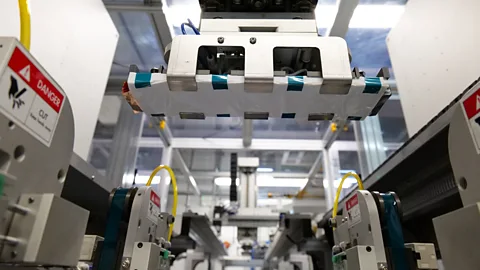
Altilium's facility is squirreled away in the unassuming English town of Tavistock. Getting here involves driving across the windswept expanse of Dartmoor, sometimes slowing to a crawl to wait for sheep to get off the road. When I arrive, I find Altilium's building on a mundane industrial estate with a tyre shop across the road – but what they're cooking up inside is anything but mundane.
In the lab I find racks of glass cylinders linked together by tubes, all filled with brightly coloured liquids – mostly vivid blues and greens – running the length of the room. Nearby, a technician wearing a white lab coat and safety glasses studies the workings of these contraptions.
This is Altilium's solvent extraction lab, where staff retrieve sought-after battery ingredients from the black mass they process here.
It all began in late 2020, but got off to a slow start. "We lost two years because of Covid," says Marston ruefully.
But in mid-2022, he and colleagues took out a lease on the Tavistock facility – at the time, an "empty shed", says chief technology officer Ben Wickham. The team built several laboratories, and began developing their recycling process on a small scale. Three years later, they are commissioning a larger plant just outside nearby Plymouth, which will supply recycled materials to battery manufacturers.
The company is one of just a handful of firms around the world that are developing methods for recycling batteries sourced from old EVs. Such firms promise to bring us one step closer to net-zero greenhouse gas emissions and also closer to a circular economy, in which almost nothing is thrown away.
"We have to remove that myth that batteries go to landfill," says Marston. As EVs have become more popular, more and more of them are now reaching the end of their useful lives. That means more exhausted batteries from those aging vehicles have become available. Recycling batteries prevents expensive – and toxic – materials getting into the environment.
Some of the other companies working on battery recycling technology are located in the US. The Inflation Reduction Act passed by President Biden's administration in 2022, which funded climate actions, has helped to motivate such efforts. Li-Cycle, a company established in 2016 which recovers critical materials from lithium-ion batteries, has plants in Canada, the US and Germany, for instance.
Hype meter
While lots of companies are working on battery recycling technologies, it's worth considering how much progress each of them have actually made to date. Altilium has, to its credit, actually manufactured battery cells using recycled materials from end-of-life electric vehicle batteries.
But this is still far from a conveyor belt churning out finished batteries ready for consumer use. Companies currently developing environmentally-friendly forms of battery recycling must show that they can compete with more polluting but established approaches, such as pyrometallurgy. Plus, processing of the black mass from old, shredded batteries often occurs in Asia today, partly because costs are lower there.
Redwood Materials, a US company with campuses in Northern Nevada and South Carolina, was established in 2017 by one of the founders of electric car company Tesla, and has partnerships with carmakers Toyota, VW and BMW. Some older materials companies have also started experimenting, notably the Texas-based Ecobat Solutions. And many other firms are now also investing in battery recycling tech.
Despite the interest, however, there's much progress to be made in the area. "The current lithium-ion battery recycling market is still in a very early industrial stage," says Xiaochu Wei, a battery recycling researcher at Imperial College London in the UK.
Last year, German chemicals firm BASF "paused" work on a battery recycling plant in Spain, though the company says it still intends to build the facility.
Part of the challenge in this field is how complex batteries are to begin with, which makes recycling them tricky.
Every battery has two main components: the cathode and the anode. When providing power to, say, a motor, the anode releases negatively-charged electrons, which flow around a circuit until they return to the battery and are absorbed by the cathode. Electrons flow in the opposite direction when the battery is charging.
In an electric vehicle battery, the cathode and anode are both thin sheets of material. The two are wrapped around each other in a spiral, like a Swiss roll with incredibly thin layers. In many battery designs, the anode is made of graphite, the same kind of carbon used in the cores of pencils. The cathode, meanwhile, often contains a variety of metals, including nickel, lithium and cobalt.
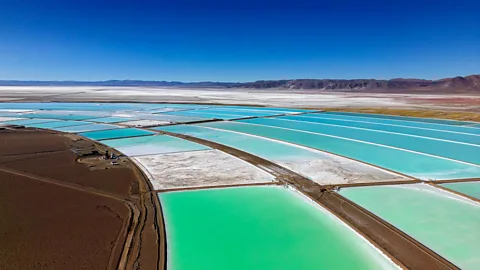
Although recycling such structures is difficult, opportunity lies in the large number of valuable materials available, all of which can be sold lucratively if extracted and purified. Somewhat frustratingly, those materials are rather closely intermingled, and many of them are dangerous: several of the metals are toxic to people and wildlife, and they also pose fire and explosion hazards.
Altilium's battery shredding process recovers graphite, originally from the anode, alongside other minerals. Getting graphite back out of a battery used to require a high-temperature process called pyrometallurgy, but this produces significant emissions, which is partly why Altilium has adopted a water-based system called hydrometallurgy. Staff soak the black mass in sulphuric acid, which allows them to filter out the graphite. This can be sold back to battery manufacturers, after some additional processing.
What's left is an acidic liquid with a variety of metals dissolved in it. Some of them – aluminium, copper and iron – are not very valuable. By tweaking the acidity, the team can force them to precipitate out as grey powder. This, Wickham says, could be sold as filler for building materials.
Now the team is in a position to extract the valuable nickel, cobalt and manganese. It recovers these one by one, mixing the liquid with kerosene and special chemicals that pull the metals out of solution. This is the step I saw with the glass tubes full of coloured liquids.
Wickham explains that Altilium takes this approach because manufacturers are constantly changing the chemical makeup of batteries. "Battery chemistry is moving fast," he says. Wickham argues that battery companies will increasingly rely on nickel, compared to other metals, because it stores more energy for a given volume. (Some emerging battery designs, however, are moving away from nickel because of its high price tag.)
By separating out individual metals, Altilium aims to supply battery manufacturers with the exact mixes they want for their new cathodes. The goal is to create a "closed-loop EV battery supply chain" in the UK, says Marston.
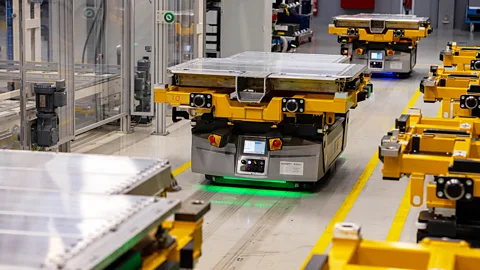
Methods that reduce old batteries to their component raw materials will be essential for sustainable economies, says Anna Hankin, a senior lecturer in chemical engineering at Imperial College London in the UK, who is working on a project funded by Altilium alongside Wei. While it's possible to regenerate used batteries by replacing chemicals lost from individual components, "at some point that process will stop working", she says. "There will come a point for every battery when its components need to be shredded."
Besides easing the transition to net zero, Marston argues that recycling EV batteries will take us a step closer to a circular economy, where, as much as possible, raw materials would be reused and recycled endlessly. This would reduce the need for extractive industries such as mining, which often damage ecosystems and pose risks to human health.
In the case of EV batteries, instead of mining more lithium, nickel and other metals from the ground, we can keep reusing the supplies we already have. Researchers have estimated that, by 2040, over half the demand for lithium and nickel for these batteries could be supplied by recycling.
In the next five to 10 years, Wei says, recycling could provide "a decent share" of the raw materials needed to make EV batteries – somewhere between 10% and 40%, she estimates. It would help if battery manufacturers redesigned their batteries to make it easier for recycling facilities to separate out the key components, she adds.
If recycling takes off, the benefits could be significant. According to a 2024 IEA report, greater recycling of critical minerals could reduce the need for new mining by as much as 40% by mid-century. The IEA notes that many governments are creating policies to encourage recycling. For instance, in 2023 the European Union introduced a new Battery Regulation, which will introduce increasingly stringent requirements for "recycling efficiency, material recovery and recycled content", beginning in 2025.
This isn't just about being environmentally friendly: there are also geopolitical motivations. In the last 20 years, the international order of things has significantly destabilised, with shocks such as Brexit and the policies of US President Donald Trump impacting global trade and international cooperation. Countries that are overly dependent on imports of critical supplies face significant risks in this new world, says Marston.
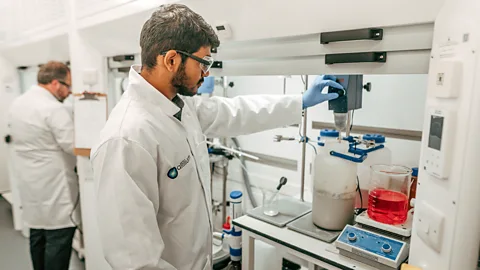
The minerals used in EV batteries will be increasingly important for countries to continue functioning. "The future economies will be the ones which control the critical minerals," says Marston. That means countries like the UK have a problem. "The UK doesn't have these minerals at scale."
In Marston's view, recycling electric vehicle batteries ensures energy security. "We see batteries which are in this country as a strategic asset in the UK," he says. Instead of sending them abroad to be recycled – possibly in a country with poor environmental and labour laws – he wants them to be recycled domestically. "If you do the processing in the UK, you add the value in the UK," he says.
The challenge for all these companies is to scale up. Altilium is currently commissioning its new larger plant which should be able to operate continuously. If that proves successful, the company has plans for two progressively larger facilities.
"If we do battery recycling at scale, we have confidence that we can produce a material which is around 20% lower cost than commercial material," says Marston. "That would look like 150,000 EV batteries per year."
--
For essential climate news and hopeful developments to your inbox, sign up to the Future Earth newsletter, while The Essential List delivers a handpicked selection of features and insights twice a week.