'Leaves on the line is like a joke - it isn't'
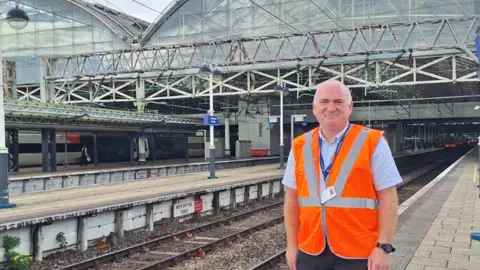
As autumn peaks, commuters will be familiar with the phrase "train cancelled due to leaves on the line".
So as October brings strong winds and heavy rain, we meet the man tasked with keeping railway lines clear of fallen leaves.
Rob Cummings has an unusual job title but a role he is passionate about.
He's now in his 10th autumn with train operator Northern and is described as the firm's seasonal performance improvement manager.
One of the main parts of his job is keeping trains running to time - no matter what England's weather throws at services.
Rather than crossing his fingers and hoping for the best, Rob has a number of advanced - and somewhat less advanced - tools to try and cut down on delays including high-tech trains, sand and steel gel, water and even lemon juice.
“Leaves on the line is a serious safety and performance issue for the railway,” he says.
“It is treated like a bit of a joke, which is frustrating.”
Train operator Northern, which is based in York and operates services across the North East, North West, Yorkshire and down into the Midlands, describes leaves as the “black ice of the railways”.
The firm has had a number of well-documented problems but Rob is focused on keeping trains safe and punctual.
He says: “You have a steel wheel on a steel rail and anything that causes low adhesion can be a big problem.”
He explains why in terms a layperson can understand: “Trains suck up leaves under the wheels and you get black surface on the wheels and if it’s wet it gets really slippery.”
High-pressure environment
The slippery leaf surface is made worse in damp or dewy conditions – but in heavy rain it clears away.
And so one of Rob’s high-tech solutions is equipment which blasts water onto the track and is being used around West Yorkshire this autumn.
“In Leeds some of the trains use Water-Trak which sprays water onto the tracks to mimic heavy rain."
Northern trains are often fitted with what are catchily-titled double variable rate sanders.
These bits of kit deploy high quantities of sand on to the rails to add friction and remove leaves.
The also have technology that prevents wheels from locking when the train is moving – which Rob describes as “a bit like ABS on a car”.
He says: “Most routes are treated once a day, but the worst lines – like the Leeds to Harrogate one – are treated twice a day,” he says.
That line is one of the worst in the country as it involves a long, steep gradient that trains need extra traction to ascend, but Rob says the route from Leeds to Manchester – through Hebden Bridge and other picturesque towns - is also top five.
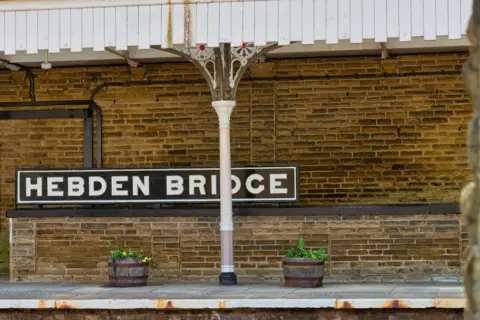
The second largest train operator in the UK, Northern provides 2,500 services a day to more than 500 stations.
Rob says it’s not just the leafy surroundings that cause the problems – it’s also the terrain.
A gentle rolling hill – like those all around West Yorkshire – leads to gradual uphill climbs with sloping sides, the perfect combination for trapping leaves and difficult driving conditions.
“The problems is that trains are steel on steel so there’s very little friction unlike a car with rubber on road,” he says.
“The contact size between the wheel and the rails is as small as a 5p piece. So 10 months of the year rail is environmentally friendly because it requires so little energy to move, but then in autumn we have this low adhesion.”
A driver's toolbox
Drivers do have a few gadgets at their disposal to make sure journeys can be completed.
“The driver can report it to the signaller and they have options to clean the rail,” he says.
“One of those is Citrusol, which is lemon juice or orange juice mixed with water.
“Or they can apply sand, which dries it up and adds friction to break up the leaves like sandpaper.”
It also affects how they drive – with Rob recommending “defensive driving”.
“Drivers must pull away more slowly and brake earlier for stations and signals to make sure they stop in time.
"This can lead to longer journey times and delays.”
Despite autumn being his focus at the moment, Rob doesn’t get the rest of the year off.
In summer he manages high temperatures, and in winter preventing journeys being affected by snow.
Last year Northern experienced 100 delay minutes due to heat, but 5,000 due to floods and fallen trees.
“Other seasonal issues are less predictable,” he says.
“For instance in summer, where rail is exposed to direct sunlight it expands.
“But this last summer was so bad that our summer review finished two hours early because there were so few problems.”
Listen to highlights from West Yorkshire on BBC Sounds, catch up with the latest episode of Look North or tell us a story you think we should be covering here.