The cities built to be reusable
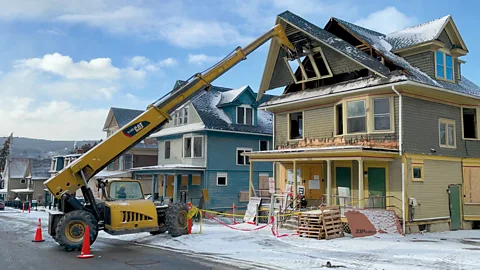
The remnants of most old buildings end up in landfill, but some cities are starting to design them for so they can be easily disassembled and repurposed from the start.
Many people now try to recycle their newspapers, plastic bottles and aluminium cans in an effort to reduce their household waste. But few of us think about the immense amount of waste produced in our names in a different way: the very buildings we live in.
The construction industry is the world's largest consumer of raw materials. New buildings alone are responsible for 5% of the world's annual greenhouse gas emissions. Most of that material will only ever be used for one building and become landfill once the building reaches the end of its lifespan, typically between 30 and 130 years.
"We're trying to, say, put the recycling out on the street, but then in the background, there's this construction industry which [in the US] produces twice the amount of waste that every one of us is producing at home," says Felix Heisel, an architect and researcher at Cornell University.
You might also like:
However, cities around the world are beginning to pay more attention to the idea of recycling building materials, and some have even passed ordinances which require building constructors to do this. Meanwhile, architects are planning ways to build new structures designed for disassembly from the get-go.
So what might a city based on these principles look like? Experts paint pictures cities of exposed wood and steel aesthetics; ones that need few outside resources to sustain their construction industries; and ones that are both greener and more flexible, able to respond to housing shortages or retrofits with ease.
But the road to these new recyclable cities is long and will require the creation of new tools, marketplaces, and incentives. Maybe even a whole new way to think about ownership and our place in the built environment.
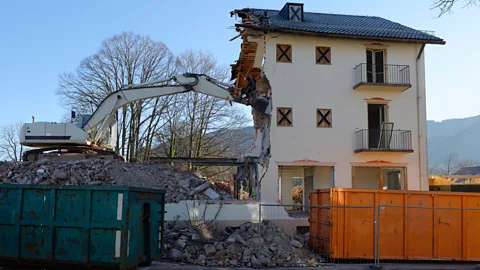
Demolishing a building is often relatively easy: a bulldozer or excavator can reduce a house to scraps within a matter of hours. But this has a significant downside: all of the material in the house, now broken and mixed together, can't really be reused and has to be either burned or transported to landfill.
It doesn't have to be this way, though. In October 2016, the city of Portland, Oregon in the United States adopted a deconstruction ordinance, requiring that residential homes built in or before 1916 (later updated to 1940) or earlier be "deconstructed", rather than demolished.
"Back in 2015, the majority of houses that came down in Portland were mechanically demolished. Today… the majority are hand-disassembled by deconstruction contractors and the materials are salvaged for reuse," says Shawn Wood, a construction waste specialist with the city.
The move was inspired by a spate of demolishings in the city that began around 2014 and concerns around wastefulness and the environmental impacts of burning debris or sending it to landfill. A number of other cities in the United States have followed suit, including Milwaukee in Wisconsin; Palo Alto and San Jose in California; and, as of September 2022, San Antonio, Texas.
Deconstruction does come with some challenges, however, as most buildings aren't designed with it in mind.
One issue is the time and labour involved. Tearing down a house might take two days altogether, but deconstruction could take 10.
If the materials recovered during deconstruction are valuable enough, their sale can make up the cost for the extra time and labour, but we often don't know what's inside buildings ahead of time, says Heisel. He is developing ways to use tools like Lidar (light detection and ranging) and construction data to help workers quickly estimate what and how much re-sellable material lie hidden behind walls. Another problem is that materials which are treated with potentially toxic chemicals or those composited, bonded or welded together into a mish-mash of wood, concrete and steel can be difficult to separate and often impossible to repurpose.
These problems could be fixed, however, if builders were to embrace an ethos known as "design for disassembly", where buildings are designed to be easily taken apart from the get-go
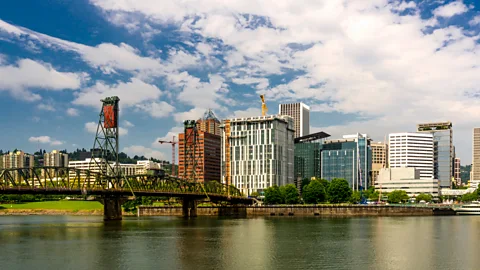
Designing for disassembly is, at its heart, a very old technique. Take the homes of nomadic people, like yurts and tipis, which are regularly taken apart due to the need to periodically move them. There are notable examples in traditional Japanese architecture as well as exhibition spaces such as the UK's Crystal Palace.
But in recent decades, some designers have pushed to incorporate plans for disassembly into office buildings, apartments and modern houses too.
So, what distinguishes a building designed for disassembly from one that isn't? One important difference might be in selecting certain more easily recycled or reused materials, like wood and steel, over others like concrete or drywall.
Another difference would be in the way parts connect. Builders would avoid hiding connections in difficult-to-reach places or make bonds that can't be broken; in place of welds and chemical adhesives, designers might focus more on removable bolts or mechanical fasteners. Even minor changes like swapping nails for screws could make it easier for future workers to take apart and reuse pieces of wood rather than binning them. Connections may also be standardised to make it easier for pieces to be swapped out or moved around.
This modular design approach would make it easier for future residents to do things like repair, add, or remove fixtures like overhead lighting or windows. Entire wall panels could be removed with the turn of a few bolts. Rooms could even be entirely repurposed with relatively little effort, with an office turning into a bedroom or even a kitchen.
This ethos has shown up in several working groups and building projects, such as the Intelligent Workplace at Carnegie Mellon University and the NASA Sustainability Base. But it also fits into a growing number of government regulations around the "circular economy" – a general term for ideas to limit humanity's impact on the environment by recycling and reusing products and materials as much as possible. Several certifications schemes, such as the UK's Breamm and Germany's DGNB, provide incentives, for example, as does the EU's circular economy action plan.
In 2021, Mayor of London Sadiq Khan's office published guidelines for large construction projects in the UK capital, requiring them to complete whole-lifecycle carbon assessments and circular economy statements before getting approval.
Andrea Charlson, built environment lead for ReLondon, a partnership organisation between the mayor's office and London boroughs, says design for disassembly fits into the London plan. Under this plan projects will need to submit circular economy statements that, among other things, demonstrate how the development will reduce material demands and "enable building materials, components and products to be disassembled and reused at the end of their useful life", says Charlson.
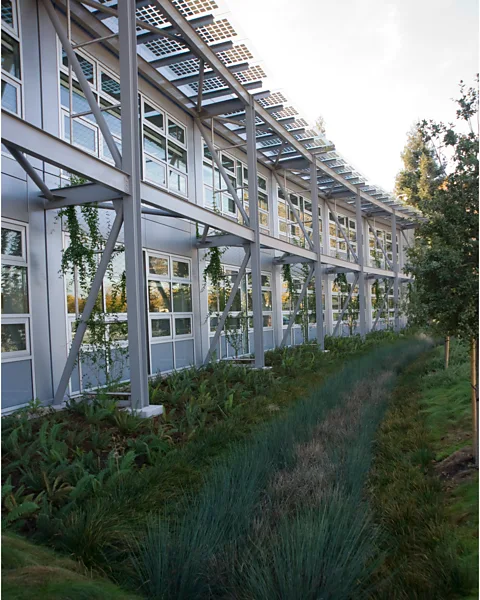
According to one analysis, designing steel structures for disassembly – where a structure is completely reused as is – can save 70% of the energy and 80% of the greenhouse gas emissions compared to a situation where the steel is completely melted down for recycling. Buildings made ready for disassembly could also be more flexible in their design during their own lifetime: interior components could be disassembled and moved around, making it easier to continue to use existing buildings as needs change.
Leonora Eberhardt, a built-environment expert at the civil engineering firm Cowi in Denmark, says that when she started in the field in 2016, many people were doubtful about the technique. "When I talked about design for disassembly, [people] told me it was never going to happen," says Eberhardt. "There's really come a change from that to now."
However, there remain challenges and limitations, cautions Eberhardt. "The barrier that was back then, and still remains today… is still the business case or the money…you may not gain anything from designing for disassembly today because what you are actually doing is securing resources for a future generation."
Part of the problem is that while designing for disassembly may save money and carbon in the long term, it can actually be more expensive now. Manufacturing and using removable steel bolts rather than irreversible welds can add to both monetary and carbon costs, for example. It can also complicate how government incentives are best portioned out, as existing building codes may prioritise and reward immediate carbon emission or waste reductions over future ones.
It also requires predicting the future, warns Freja Nygaard Rasmussen, an expert at the Norwegian University of Science and Technology, and lead author of a lifecycle assessment of a hypothetical design-for-disassembly building in 2019. The benefits of temporary or short-lived buildings are more obvious, she says, "but when we're dealing with service lifespans of 150 years, that's where I can be a bit critical". A significant portion of a building's environmental footprint is tied up in long-lived materials such as steel and concrete, but their long lifespan makes it hard to confidently predict whether we can actually reuse them at all.
"Would we even design buildings with these type of elements in 150 years, right?" asks Rasmussen. "Looking 150 years back in time, the building practices were quite different from today. So the assumption that the concrete structures we built today will be used in 100 years, exactly as they are, is quite dubious."
In her view, the best value might come from focusing on components that we know may have shorter lifespans, like windows. Both Eberhardt and Rasmussen caution that, depending on the analyses used, developers could also try to claim future benefits in order to greenwash their current environmental impact.
There are a number of other challenges to overcome before design for disassembly will see widespread use. A robust marketplace would need to be developed for building owners to buy and sell reclaimed material. The types and origins of these materials would also need to be traceable and documented, such as through databases or material passport systems which gave information on the material which helps guide it to reuse.
Another problem is that some infrastructure, like paved roads, may not fit well within the "design for disassembly" framework.
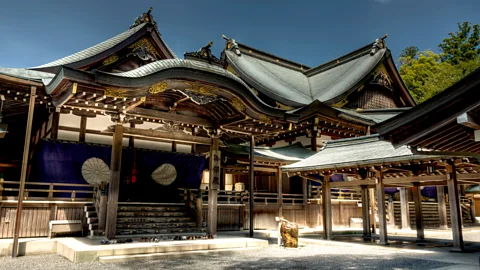
Nevertheless, many experts do see promise in the technique and can envision what a city completely based on design for disassembly might look like. "When I think about a design-for-disassembly city, I actually think about The Lego Movie," says Eberhardt – each and every building block fits together and together they can be reshaped into countless forms.
Carbon Count
The emissions from travel it took to report this story were 0kg CO2. The digital emissions from this story are an estimated 1.2g to 3.6g CO2 per page view. Find out more about how we calculated this figure here.
Other experts speak about the societal or health benefits of cities centered around reusing and sharing resources – such as having more equitable economies and less potentially hazardous waste to deal with – or cities that could easily adapt to housing shortages by simply reconfiguring existing buildings.
Rasmussen describes her image of a young couple in a small flat that, rather than moving as they had children, could simply buy adjacent flat units, disassembling the walls to make more space, only to shrink the unit again years later when their now-grown children moved out.
Experts also note that cities could look aesthetically closer to the style known as high-tech or structural expressionism, where the internal structure is more accessible and visible. "You would appreciate the raw materials, just as they are," says Eberhardt. Flats could also have less paint and wallpaper and more bare wood on the walls.
Ultimately, the way we look at houses and, indeed, cities as a whole could change if our buildings were designed to be disassembled, adds Eberhardt. Instead of seeing the built environment as something to own, it could become one more thing to shepherd and pass down to the next generation.
--