The promise of batteries that come from trees
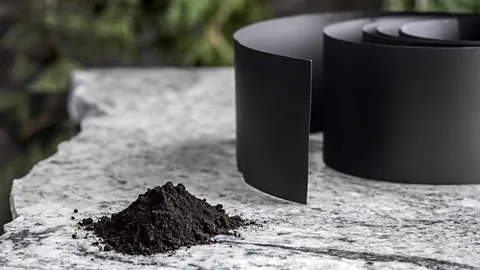
As demand for electric vehicles soars, scientists are searching for materials to make sustainable batteries. Lignin, the stuff that makes trees woody, is shaping up to be a strong contender.
About eight years ago, a major paper producer in Finland realised the world was changing. The rise of digital media, a fall in office printing and the dwindling popularity of sending things by post – among other factors – meant that paper had embarked on a steady decline.
Stora Enso, in Finland, describes itself as "one of the largest private forest owners in the world". As such, it has a lot of trees, which it uses to make wood products, paper and packaging, for example. Now it wants to make batteries as well – electric vehicle batteries that charge up in as little as eight minutes.
The company hired engineers to look into the possibility of using lignin, a polymer found in trees. Around 30% of a tree is lignin, depending on the species – the rest is largely cellulose.
"Lignin is the glue in the trees that kind of glues the cellulose fibres together and also makes the trees very stiff," explains Lauri Lehtonen, head of Stora Enso's lignin-based battery solution, Lignode.
Lignin, a polymer, contains carbon. And carbon makes a great material for a vital component in batteries called the anode. The lithium ion battery in your phone almost certainly has a graphite anode – graphite is a form of carbon with a layered structure.
Stora Enso's engineers decided that they could extract lignin from the waste pulp already being produced at some of their facilities and process that lignin to make a carbon material for battery anodes. The firm is partnering with Swedish company Northvolt and plans to manufacture batteries as early as 2025.
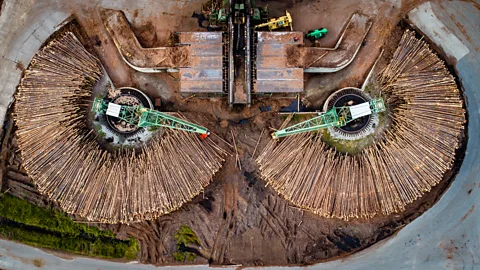
With more and more people buying electric cars and storing energy at home, the global appetite for batteries is expected to grow sharply in the coming years. As Lehtonen sees it, "the demand is just mind-blowing".
In 2015, a few hundred additional gigawatt hours (GWh) were required every year across the world's battery stocks – but this will rocket to few thousand additional GWh required annually by 2030 as the world moves away from fossil fuels, according to management consultancy McKinsey. The problem is that the lithium ion batteries we rely on today largely depend on environmentally damaging industrial processes and mining. Plus, some of the materials for these batteries are toxic and difficult to recycle. Many are also sourced in countries with poor human rights records.
Making synthetic graphite, for example, involves heating carbon to temperatures of up to 3,000C (5,432F) for weeks at a time. The energy for this often comes from coal-fired power plants in China, according to consultancy Wood Mackenzie.
The search is on for sustainable battery materials that are more widely available. Some say we can find them in trees.
Generally, all batteries need a cathode and anode – the positive and negative electrodes, respectively, between which charged particles called ions flow. When a battery is charged, lithium or sodium ions, for example, transfer from the cathode to the anode, where they settle like cars in a multi-storey car park, explains Jill Pestana, a California-based battery scientist and engineer currently working as an independent consultant.
"The main property that you want in this parking structure of a material is that it can easily take in the lithium or sodium and let it leave, and it doesn't crumble apart," she explains.
When the battery is discharged in order to power something like an electric car, the ions move back to the cathode after releasing electrons – the electrons move through the wire in an electrical circuit, transferring energy to the vehicle.
Graphite, Pestana says, is a "spectacular" material because it works so well as a reliable anode that enables such reactions to take place. Alternatives including lignin-derived carbon structures have a fight on their hands to demonstrate that they are up to the job.
There are multiple firms exploring lignin's potential in battery development, however, such as Bright Day Graphene in Sweden, which makes graphene – another form of carbon – from lignin.
Lehtonen extols the virtues of his firm's carbon anode material, which Stora Enso has named Lignode. He won't reveal exactly how the company turns lignin into a hard carbon structure, or what that structure is, exactly, except to say that the process involves heating the lignin – but to temperatures nowhere near as high as those required for synthetic graphite production.
One important feature of the resulting carbon structure is that it is "amorphous", or irregular, says Lehtonen: "It actually allows a lot more mobility of the ions in and out."
Stora Enso claims that this will help them make a lithium ion or sodium ion battery that can be charged in as little as eight minutes. Fast charging is a key goal for developers of electric vehicle batteries.
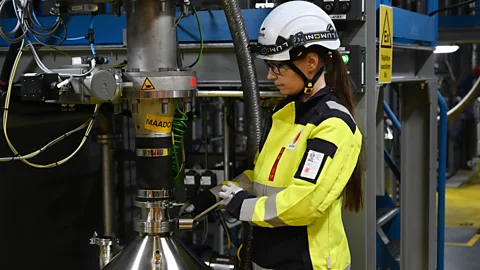
Separate research into lignin-derived carbon anodes, by Magda Titirici at Imperial College London in the UK and colleagues, suggests that it is possible to make conductive mats containing intricate, irregular carbon structures with lots of oxygen-rich defects. These defects appear to heighten the anode's reactivity with ions transferred from the cathode in sodium ion batteries, says Titirici, which in turn shortens charging times: "This conductive mat is fantastic for batteries."
Wyatt Tenhaeff, at the University of Rochester in New York State, has also made lignin-derived anodes in laboratory settings. Lignin is "really cool", he says, because it is a byproduct that could have many potential uses. In experiments, he and his colleagues found that they could use the lignin to make an anode with a self-supporting structure, which didn't require glue or a copper-based current collector – a common component in lithium ion batteries. Despite the fact that this could reduce the cost of lignin-derived carbon anodes, he is sceptical that they can compete commercially with graphite anodes.
"I just don't think it's going to be a big enough step-change in terms of cost or performance to replace the entrenched graphite," he says.
There's also the issue of sustainability. Chelsea Baldino, a researcher at the International Council on Clean Transportation, says that so long as the lignin used for anode production is extracted as a byproduct from the paper-making process, then additional trees won't be chopped down in order to make batteries.
A spokesman for Stora Enso confirms that, currently, all lignin the company uses is "a side stream of the pulping process", and utilising it does not increase the number of trees felled or volume of wood used in pulp-making.
Anyone seeking to make anodes from lignin must ensure that the forestry from which that lignin is sourced is also sustainable, however, adds Pestana. "If the pulp industry isn't sustainable, then the material itself isn't a sustainably derived material," she explains.
According to Stora Enso's 2021 annual report , the company "knows the origin of all the wood it uses and 100% comes from sustainable sources".
There is at least one other way that lignin could be used in batteries, besides anodes. In April, a research team in Italy published a paper about their efforts to develop a lignin-based electrolyte. This is the component that sits between the cathode and anode – it helps ions flow between the electrodes but also forces electrons to take the desired path through the electrical circuit to which the battery is connected. In other words, it prevents the electrons from simply bouncing between the electrodes, which would leave your smartphone as dead as a doornail.
Carbon Count
The emissions from travel it took to report this story were 0kg CO2. The digital emissions from this story are an estimated 1.2g to 3.6g CO2 per page view. Find out more about how we calculated this figure here.
You can get polymers for electrolytes from oil, says Gianmarco Griffini at the Polytechnic University of Milan, but he adds that it would be beneficial to find alternative, sustainable sources instead.
He explains that the idea of using lignin arose after he and colleagues experimented with using the material in solar panels – with slightly underwhelming results. "The efficiencies you get in solar cells are relatively limited because lignin is brown, so it actually absorbs some light," he explains. In batteries, that doesn't matter.
For anode production, lignin is heat-treated to break it into its constituent carbons. But Griffini, a self-described "polymer guy", says he prefers to use it in its polymer form. With this in mind, he and colleagues developed a gel polymer electrolyte that aided the movement of ions in an experimental potassium battery. "It actually came out pretty nicely," he says.
The commercial viability of all these ideas is yet to be proven. Titirici adds however that, in theory, you could make a battery that uses polymers from lignin in the electrolyte as well as lignin-derived carbons in the anode.
Maybe you could even use it to power the wooden electronic components described in a paper earlier this year. Perfect tech for your treehouse, right? Or would that be going too far?
--